Defining Pandametrics:
Parametric
design – defining a series of design processes by a set of adjustable
parameters
Zen
– enlightenment through meditation, self contemplation and intuition
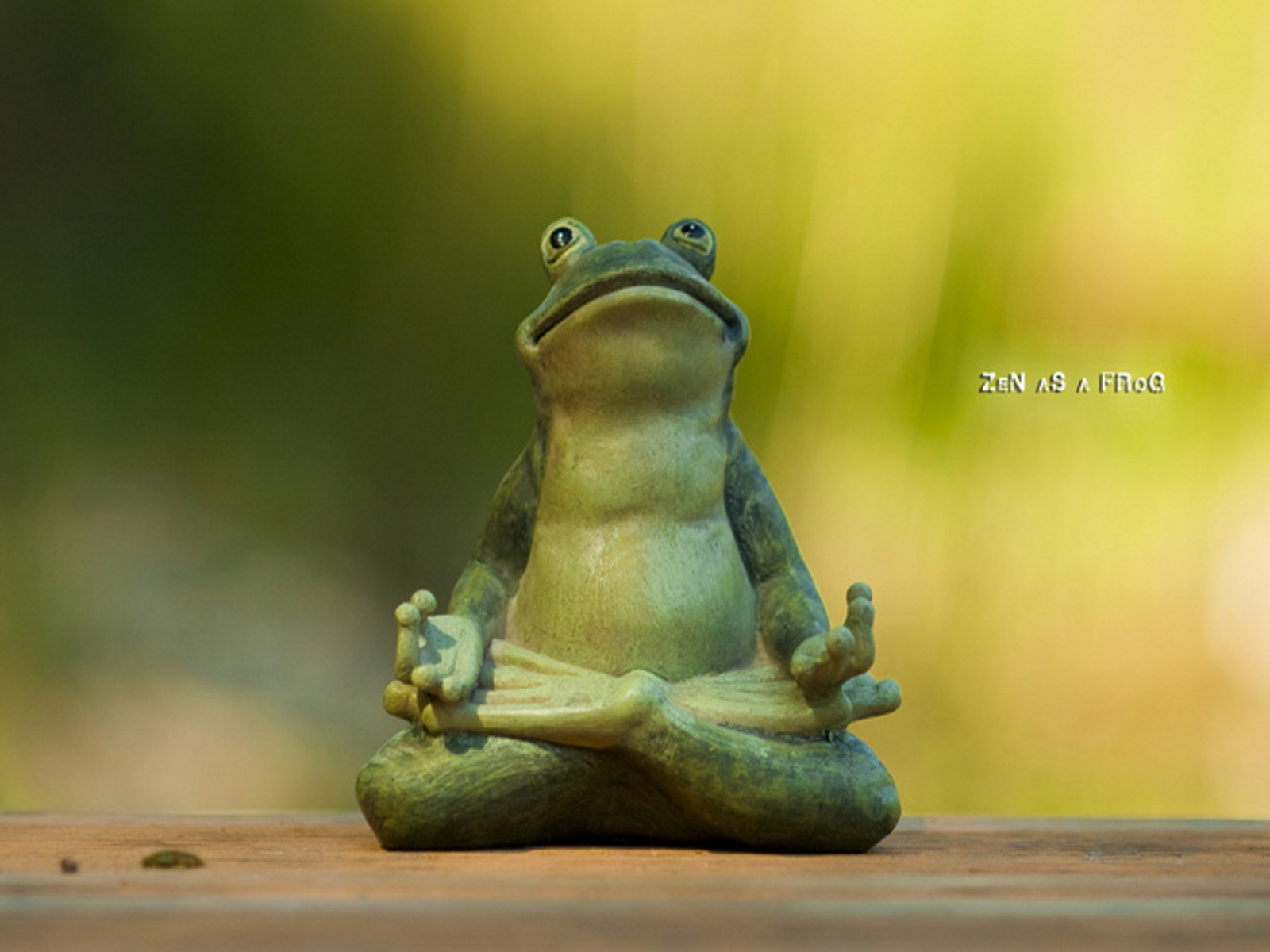 |
Not a panda...but pretty Zen |
In
structural engineering when we talk about parametrics we are traditionally
talking about our modelling and design workflows, where the input parameters
are a series of geometric definitions such as intersecting circles, variable
frame settings, definable surface forms etc.
However,
we often meet many definitions of parametric throughout the construction industry,
just as we meet many definitions of BIM (an argument for another day)!
The
zen art of parametrics, or Pandametrics as we like to call it (in true naming
workflows and software after animals fashion), is using our experience and
intuition to pick the right parameters for the most holistically efficient
design workflow.
A brief aside, As I'm writing this at this years Autodesk University 2015 I'll take this opportunity to point out that architects and engineers who have been using parametric design, you're the choir and this is piece is going to come across as me preaching what you already know, although hopefully with a few talking points or bits you've not considered. Primarily this is written from the point of view of talking to those who haven't used parametric design but are considering making the plunge. Anyway, I digress, back to the content...
Why
Panda? – Some Chinese philosophers
believe that the black and white of the Panda represents the opposing forces of
Yin and Yang and in the time honoured tradition of using animal names for
workflows and plugins we have focused on the Panda. Is there an animal more zen
that representing the balanced peace and harmony of parametric design?
 |
Zen Panda |
Let's
expand that…
When
I am asked to create a parametric model my first task is to work out what the
key adjustable inputs are that can optimise our solution and most importantly
what constitutes ‘optimised’.
We
should talk about what we mean by optimised as it forms the foundation of the
parametric process. In my experience, optimised in terms of building structures
could be any number of things, for example:
•
A found form which produces pure structures such as a pure tension structure,
or a pure arch.
•
a form which is confined by specific criteria such as avoiding ponding, or
minimum curvature.
•
a structure which can be mapped to a specific aesthetic but adjusted for
material performance.
•
workflows which improve interoperability speeds to allow rapid prototyping and
analysis.
•
a structure which is optimised for alternative key performance indicators such
as cost, or additive material tonnage, or reductive material tonnage, or
aesthetic, or energy performance, or user comfort…..the list goes on ad
infinitum.
Benefits
of Parametric Design
The
largest benefit of producing a parametric model should come from an
understanding of
- the specific outcome you are looking to achieve;
and
- which small group of inputs with best help you
achieve this.
One
thing I can say for certain is that creating a parametric design process
without fully understanding both of these will end in something too unwieldy to
be practical or so inflexible it finds itself on the scrap heap the second your
input requirements change.
The
basic benefit of all parametric design (sweeping statement coming) should be to
make your design processes more efficient and anything that has to be binned
off at the first hurdle because it's too inflexible fails even this simple test.
And
I’m gonna stop right there… right before launching into the do’s and don’ts of
parametric modelling, mainly because this blog is getting a bit on the long
side, but also because it means when we return for the thrilling conclusion
there will also be a hint of the workflows we’ve developed and a lead in to the
free bit of software for download that Ricky has been pioneering….watch this
space